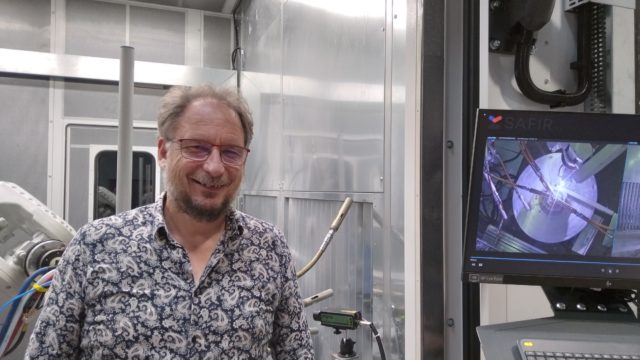
IRCER – Plateforme SAFIR par Alain Denoirjean
Alain Denoirjean : SAFIR, un outil technologique de pointe
Alain Denoirjean, Directeur de recherche CNRS à l’IRCER et Responsable de SAFIR*, nous présente cette plateforme technologique à haute performance.
C’est quoi SAFIR ?
C’est une plateforme technologique qui réunit sous un même toit les compétences de trois entités – SAFRAN, leader dans la fabrication de pièces aéronautiques, Oerlikon un des leaders mondiaux en construction de machine de traitement de surface, l’IRCER, laboratoire mondialement reconnu en science des matériaux et des procédés céramiques et de traitement de surface par voie sèche.
Comment est venue l’idée d’une telle association ?
L’IRCER travaille depuis 30 ans avec ces industriels qui pour rester leader dans leur secteur ont décidé de s’associer à l’Institut pour créer en 2020 un laboratoire de recherche commun « Prothéis » puis, en 2021, une plateforme technologique « SAFIR » pour abriter le matériel nécessaire.
Qu’y fait-on ?
La plateforme intègre les activités du laboratoire Prothéis qui travaille sur les applications aéronautiques, mais elle propose également d’autres activités. En effet, la Région qui a financé la moitié de l’équipement (donc la moitié de 5,6 M d’€), désirait qu’on se diversifie. On y fait donc de la recherche, mais aussi de la maturation industrielle, de la prestation industrielle (SAFIR est accessible aux entreprises souhaitant mener des études), et de la formation.
SAFIR permet sur un même site de partir de l’idée et d’aller jusqu’à la réalisation de la pièce prototype réelle pour la démonstration industrielle du concept initial. A l’issue de cette étape, et de la validation par l’industrie, cela peut être pleinement mis en application dans des conditions de production industrielle.
Pouvez-vous nous donner quelques exemples de projets que vous traitez ?
Par exemple, une activité en fort développement est la réparation de pièces en alliage d’aluminium usées afin d’éviter de les jeter et de pouvoir les réutiliser. Cela répond aux attentes sociétales de réduction de la consommation de matière première par accroissement de la durabilité des pièces. Sont concernées par exemples les roues du train d’atterrissage.
On étudie également la résistance des matériaux qui subissent des dégâts causés par des poussières équivalentes à du sable en composition d’oxyde (CaO, MgO, SiO2, Al2O3). Ces compositions sont appelées CMAS.
Les avions peuvent aspirer ce CMAS dans trois cas : ils traversent un nuage d’éruption volcanique, ils volent près d’une étendue de sable, ou ils atterrissent sur un tarmac en béton qui produit ce CMAS. Ce CMAS fond autour de 1200 °C, température que l’on retrouve au voisinage des derniers éléments de compression du réacteur (Turbine HP). Lorsqu’il fond, il corrode et pénètre la couche de protection thermique et lorsqu’il refroidit, il fissure le dépôt barrière thermique ce qui endommage le réacteur. On souhaite donc modifier les matériaux pour qu’ils résistent à la corrosion, et qu’ils empêchent l’infiltration du liquide dans la barrière thermique. Nous mettons au point le moyen d’essai pour valider la résistance du matériau.
Nous gérons entre 300 000 € et 500 000 € par an de volume d’affaires, essentiellement orienté autour de l’aéronautique. A titre d’exemple, une des thématiques principales est la protection des composites aéronautiques organiques qui posent des problèmes de non résistance à l’usure, au foudroiement, à l’abrasion, aux températures extrêmes.
Pourquoi employer ces matériaux organiques alors ?
Parce qu’ils sont moins lourds que les matériaux métalliques utilisés jusque-là.
Le but de SAFRAN est d’alléger les matériaux pour construire des avions plus légers, donc moins polluants, moins bruyants avec des composites plus résistants. Bref, des avions plus respectueux de l’environnement.
*Surface Advanced Functionalization For Industry And Research