L’Institut de Recherche sur les Céramiques
L’IRCER est spécialisé dans l’étude et le développement de procédés innovants autour des céramiques.
Implanté au cœur de la France, en Nouvelle-Aquitaine, l’IRCER innove dans le développement de céramiques de très hautes technologies en répondant aux nouveaux enjeux industriels et sociétaux (énergie, technologies de l’information et de la communication, santé, écomatériaux…).
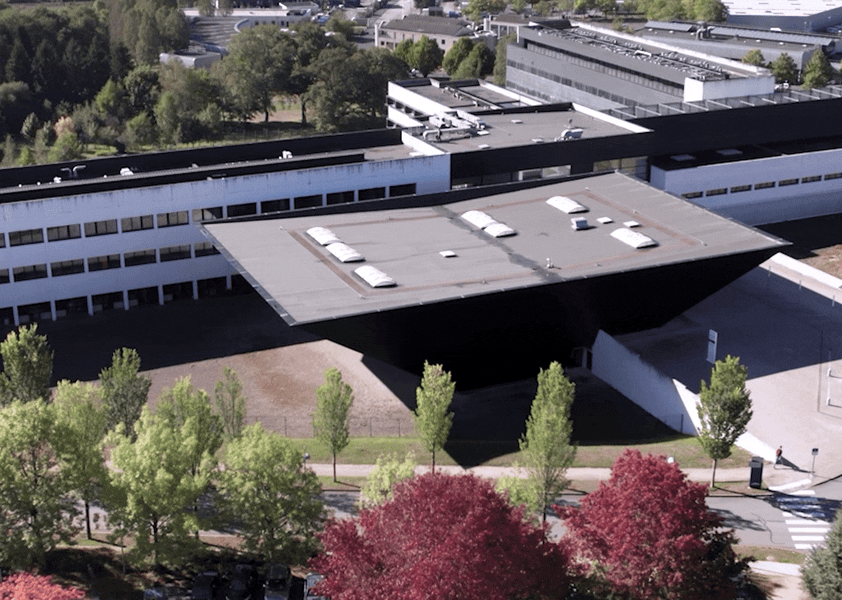
Nos dernières actualités
Navigating a Greener Sky
Du 12 au 14 nov, l’IRCER a organisé le congrès “Symposium on Advances in Thermal Spray and PVD Coatings for Aerospace Industries".
Maxime Gaudin remporte le prix du public du concours photo Regard[e] la science !
Maxime Gaudin est un des lauréats du concours photo Regard[e] la science.
L’IRCER organise un séminaire dédié au Développement Durable
Ce mercredi 23 octobre, l'IRCER a organisé un séminaire dédié au développement durable.
Inauguration LABCOM LIRYS (Imerys – IRCER)
Le 3 juillet 2025, le LABCOM LIRYS (Projet-ANR-23-LCV2-0005 - Imerys / IRCER) a été inauguré lors de la convention d'affaires du Réseau Céramique à Limoges.
Le 17ème Colloque sur les Arcs Electriques (CAE) à Limoges !
Du 17 au 18 mars 2025, l'IRCER a organisé un Colloque sur les Arcs Electriques (CAE) à Limoges.
Une journée Intelligence Artificielle à l’IRCER
L'Institut de Recherche sur les Céramiques a organisé une journée dédiée à l'Intelligence Artificielle le 14 mars 2025.
Lech Pawlowski publie un livre intitulé « Physical Deposition Methods for Films and Coatings »
Lech Pawlowski vient de publier un nouvel ouvrage.
L’IRCER s’associe à Imerys Aluminates à travers un nouveau labcom « LIRYS »
LIRYS développe des solutions innovantes et durables pour les dépôts céramiques en couches minces
Satoshi TANAKA, professeur invité à l’IRCER
En décembre 2024, l'IRCER, avec le support du le LABEX ∑-LIM et de l’EUR TACTIC, a eu l’honneur d’accueillir le Pr. Satoshi TANAKA, en tant que professeur invité.
Navigating a Greener Sky
Du 12 au 14 nov, l’IRCER a organisé le congrès “Symposium on Advances in Thermal Spray and PVD Coatings for Aerospace Industries".
Maxime Gaudin remporte le prix du public du concours photo Regard[e] la science !
Maxime Gaudin est un des lauréats du concours photo Regard[e] la science.
L’IRCER organise un séminaire dédié au Développement Durable
Ce mercredi 23 octobre, l'IRCER a organisé un séminaire dédié au développement durable.
Inauguration LABCOM LIRYS (Imerys – IRCER)
Le 3 juillet 2025, le LABCOM LIRYS (Projet-ANR-23-LCV2-0005 - Imerys / IRCER) a été inauguré lors de la convention d'affaires du Réseau Céramique à Limoges.
Le 17ème Colloque sur les Arcs Electriques (CAE) à Limoges !
Du 17 au 18 mars 2025, l'IRCER a organisé un Colloque sur les Arcs Electriques (CAE) à Limoges.
Une journée Intelligence Artificielle à l’IRCER
L'Institut de Recherche sur les Céramiques a organisé une journée dédiée à l'Intelligence Artificielle le 14 mars 2025.
Nos évènements
Nos axes de recherche
L’IRCER réalise des études autour de quatre axes de recherche et de deux thèmes transversaux « intelligence artificielle, science des matériaux et procédés » et « Matériaux, procédés céramiques et développement durable » rassemblant des chercheurs et enseignants-chercheurs en chimie, physique et mécanique.
AXE 1 - Procédés céramiques innovants
Lire plus →
AXE 2 - Procédés plasmas et lasers
Lire plus →
Intelligence artificielle pour la science des matériaux et les procédés céramique
Lire plus →
AXE 3 - Organisation structurale multiéchelle des matériaux
Développement durable et recyclabilité
Lire plus →
AXE 4 - Céramiques sous contraintes environnementales
Lire plus →
L’IRCER en chiffres
Membres (chercheurs, enseignants-chercheurs, ingénieurs, techniciens, doctorants et post-doctorants)
Plateformes technologiques : CARMALIM, SAFIR
Laboratoires communs avec le CEA le Ripault, IMERYS, SAFRAN et OERLIKON
International Research Projects (IRP) : FRESH, B3Lab
Start-ups créées et 26 brevets dont 6 licences exclusives et 2 cessions de propriétés depuis 2015
Laboratoire d’Excellence ∑-LIM avec l’Institut XLIM
Des partenariats et collaborations industrielles pour une filière d’excellence céramique
L’IRCER appartient à un écosystème complet d’innovation autour de la céramique, principalement basé à Limoges, incluant des pôles de compétitivité, des centres de transfert et des structures de valorisation.
Le centre de recherche sur les céramiques a une grande expérience, des partenariats universitaires et industriels aux niveaux national et international. Certains partenariats de long terme ont abouti à la mise en place de laboratoires communs.
Les contrats de recherche industriels constituent un quart du budget annuel du laboratoire, représentant ainsi sa principale ressource financière.
Publications
L’institut contribue au développement de la recherche en France et à l’international, autour des céramiques : procédés physiques de dépôt par plasmas et/ou lasers, voie sol-gel, impression numérique 2D/3D, procédés de frittage non conventionnels, stéréolithographie, chimie de matériaux, biologie, etc.
Nos dernières publications